The drop test is one for the most damaging product-use tests that design engineers have to consider when creating a new product or optimizing a current one. Mobile devices such as smart phones and tablets, with their rigid structural frames and glass displays, are especially susceptible to failure when dropped onto a solid surface as high g-forces are distributed throughout the structure. Packaged liquids, especially those where the product weight is high relative to the container, are also susceptible to leakage and material failure after a drop event. Package buckling creates large material strain levels that can lead to catastrophic material failure and leakage.
Compounding the severity of the drop event on consumer packaged goods (CPG) and electronic products are the difficulties design engineers face in understanding failure modes and meeting project deadlines with lengthy trial-and-error test cycles. Even creating test prototypes that accurately represent production products is challenging, and drop testing, with many possible impact angles and scenarios, is inherently time consuming.
Fortunately today several popular commercial software packages have drop test analysis capabilities, including ANSYS, ABAQUS, LS-DYNA, and others. Drop test simulation tools allow Modeling and Simulation engineers to quickly predict product drop performance and modify the design to meet the specified use criteria. The accuracy of drop test simulations are dependent on many criteria, especially the knowledge and experience of the analyst, accurate FEA Material Properties, and are most often accompanied by corroborative physical testing.
Learn more about ASTM Drop Test Standards.
Water Jug Lightweighting
"Lightweighting" is a process where an existing container is optimized to meet defined structural requirements while using minimum material. A standard water jug consists of a thin-walled, blow-molded container with a screw-on cap, and creating an optimum design requires fluid-structure interaction analysis capabilities. Because of very high production volumes, reducing the material volume by even a few percent produces significant cost savings. Its response to being dropped onto a rigid floor is complex, and is dependent on many parameters including the bottle shape, material properties and thickness profile, amount of liquid in the container and impact orientation.
In this example, Kinetic Vision simulation analysts utilized LS-DYNA to perform a drop test simulation considering different volumes of liquid in the container, with the goal of minimizing the part material volume while also meeting the product functional requirements.
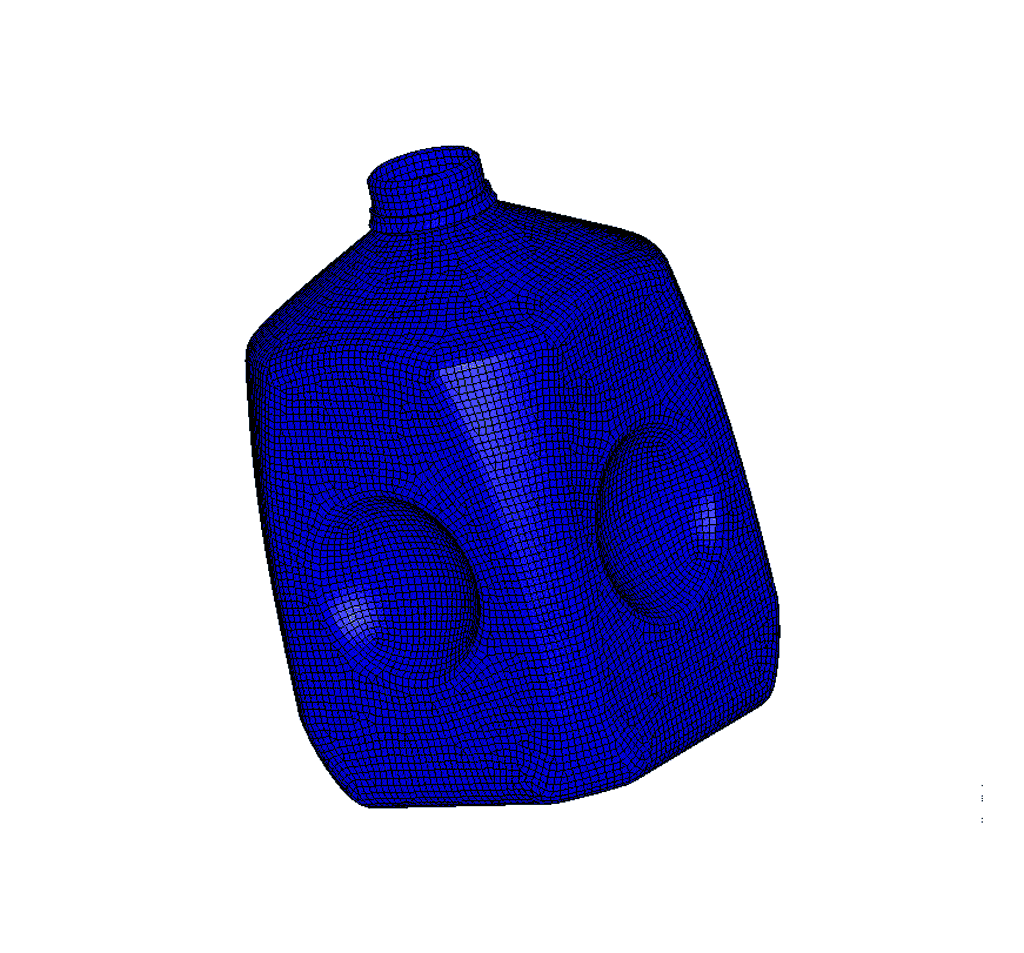
Packaging Design for E-Commerce
Online shopping has surpassed sales in retail stores and the gap is expected to widen. Amazon Prime membership is estimated to be 80 million people in the U.S. alone. Online shipments of household items have increased dramatically, especially among millennials and those in high-population urban environments. That reality has forced many CPG companies to re-evaluate their product packaging, as more products are shipped individually or with other items instead being transported in bulk to warehouses and distribution centers. This paradigm shift has created new shipping and handling challenges that could impact package performance and consumer brand satisfaction.
In this example, LS-DYNA was used to perform drop test simulations of a liquid detergent bottle when dropped from five feet on the closure cap. Simulation results were compared to high-speed video of physical tests to corroborate the simulation model. Of particular interest was bottle leakage and material fracture. Complexities in the study included contact and material nonlinearities, structural buckling, material failure modeling and fluid-structure interaction.

Mobile Phone Drop Test Simulation
This drop test simulation was used to study product performance for a four-foot corner drop onto a rigid surface. LS-Dyna's crack propagation method XFEM (eXtended Finite Element Method) was utilized for crack fracture and evolution prediction considering material failure strain under tensile, compressive, and shear loading. Various design parameters were modified to improve the product's drop performance.