Injection molding simulation, often called mold filling analysis, predicts how resin will flow through a mold and identifies problem areas in the part or mold designs. Commons problems like warping, sink marks, weld lines, short shots, fiber orientation, etc. are very time consuming to troubleshoot via trial-and-error mold modification and testing. Many of these issues can be predicted and improved over a period of a few days using molding simulation, versus several weeks or months for manual mold iterations. Mold design parameters such as gate location(s), parting lines and cooling properties can be modeled and optimized, as can the process parameters such as temperature, pressure, and timing. All have an large impact on the finished part.
Kinetic Vision's injection molding simulation services can greatly shorten mold development time and allow for shorter cycle times, more consistent part quality and more reliable parts.
See also Product Design + Development.
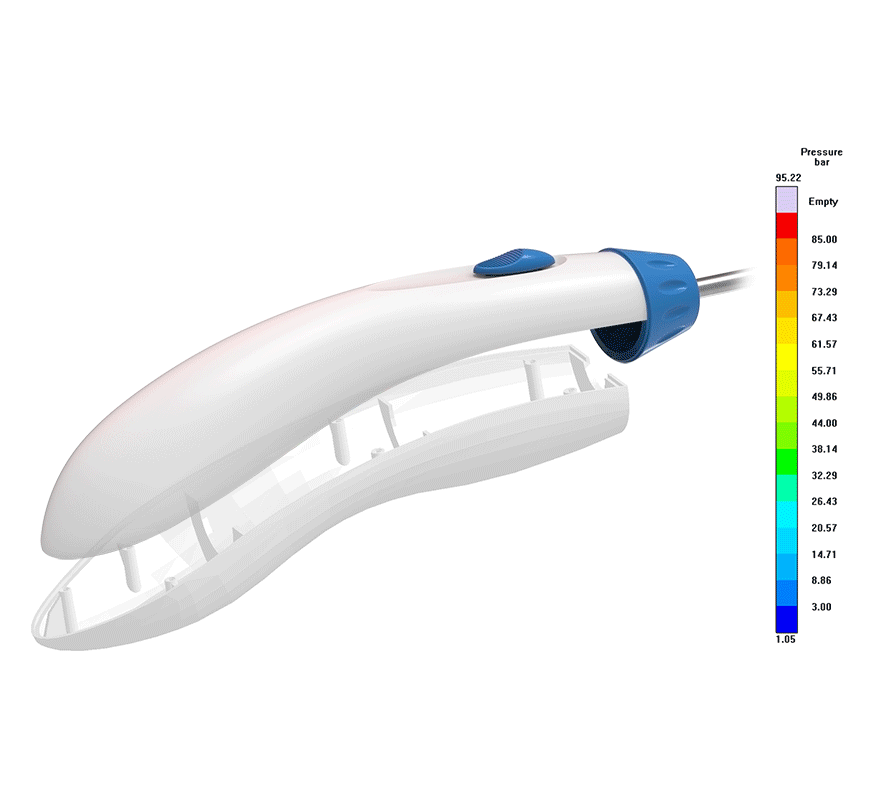
Closure Cap Mold-Filling Study
In this injection molding simulation, a cap design was analyzed to predict the mold fill time, part warpage and locations of weld lines. The part design was optimized by Kinetic Vision to ensure that cycle times were minimized due to the high annual part volume and target cost. Another key feature verified through the filling analysis was the performance of the living hinge. Proper design features were developed that allowed for adequate part filling while maintaining the structural integrity of the hinge. Part warpage was also studied to ensure proper mating of the sealing surfaces.