Simulation validation is essential to confirm the accuracy of modeling and simulation results, and is often difficult for transient events such as shock, vibration and impact. Kinetic Vision is equipped with the latest technologies to test product dynamic performance and tune simulation models to match real-world performance. Using multiple sensors and hi-speed video, precise physical data is collected and post-processed. By validating simulation models, users can gain valuable insights into how best to utilize computer tools to represent real-world product performance.
Simulation Validation: Bottle Top Load Crush Strength
Consumer Packaged Goods (CPG) companies manufacture millions of blow-molded bottles a year, and are constantly introducing new products into the marketplace. These bottles are designed to provide the necessary structural strength for shipment and consumer use, but are also optimized for minimum plastic use as small per-bottle material savings can add up to tens of millions of dollars of cost savings annually. Modeling and Simulation is an invaluable tool in new product development and optimization of existing packaging, but correctly modeling the thin-wall buckling and nonlinear material properties can be a challenge for most engineering analysts. In addition, there are simulation subtleties that greatly affect the calculated results.
Because of the extreme nonlinear buckling behavior of thin-walled structures, having an accurate understanding of bottle wall thickness is critical. In this example an actual bottle's wall thickness distribution was measured using two common methods: Magna-Mike (a magnetic/hall effect sensor) and Computed Tomography (CT) scanning. In addition, a simulation was performed using a uniform wall thickness model where the FEA model matched the actual bottle mass. Contour plots of model thickness for the three modeling approaches are shown below.
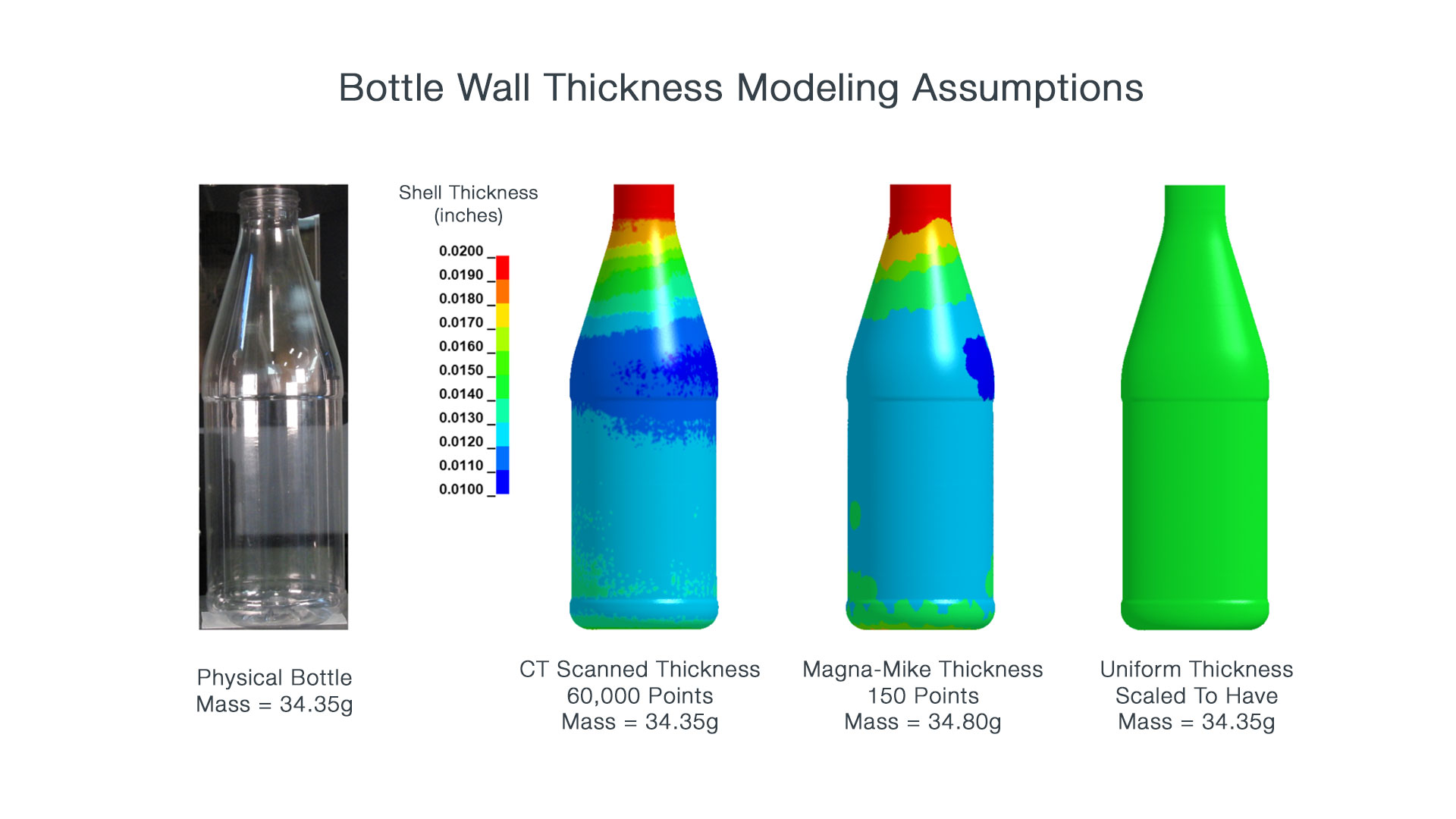
Results of the top crush load simulations are shown below. Using the 60,000 wall thickness values from the 3D CT scan the crush load matched within 2.0% of the measured value. The Magna-Mike measured thicknesses resulted in 29% error, and the constant wall thickness model (which most analysts would assume without any knowledge of the true thickness distribution) resulted in 41% error! This demonstrates the input-parameter sensitivity of extremely nonlinear simulation problems. The uniform wall thickness assumption is problematic not only that produced erroneous results, but was also non-conservative from an engineering perspective.
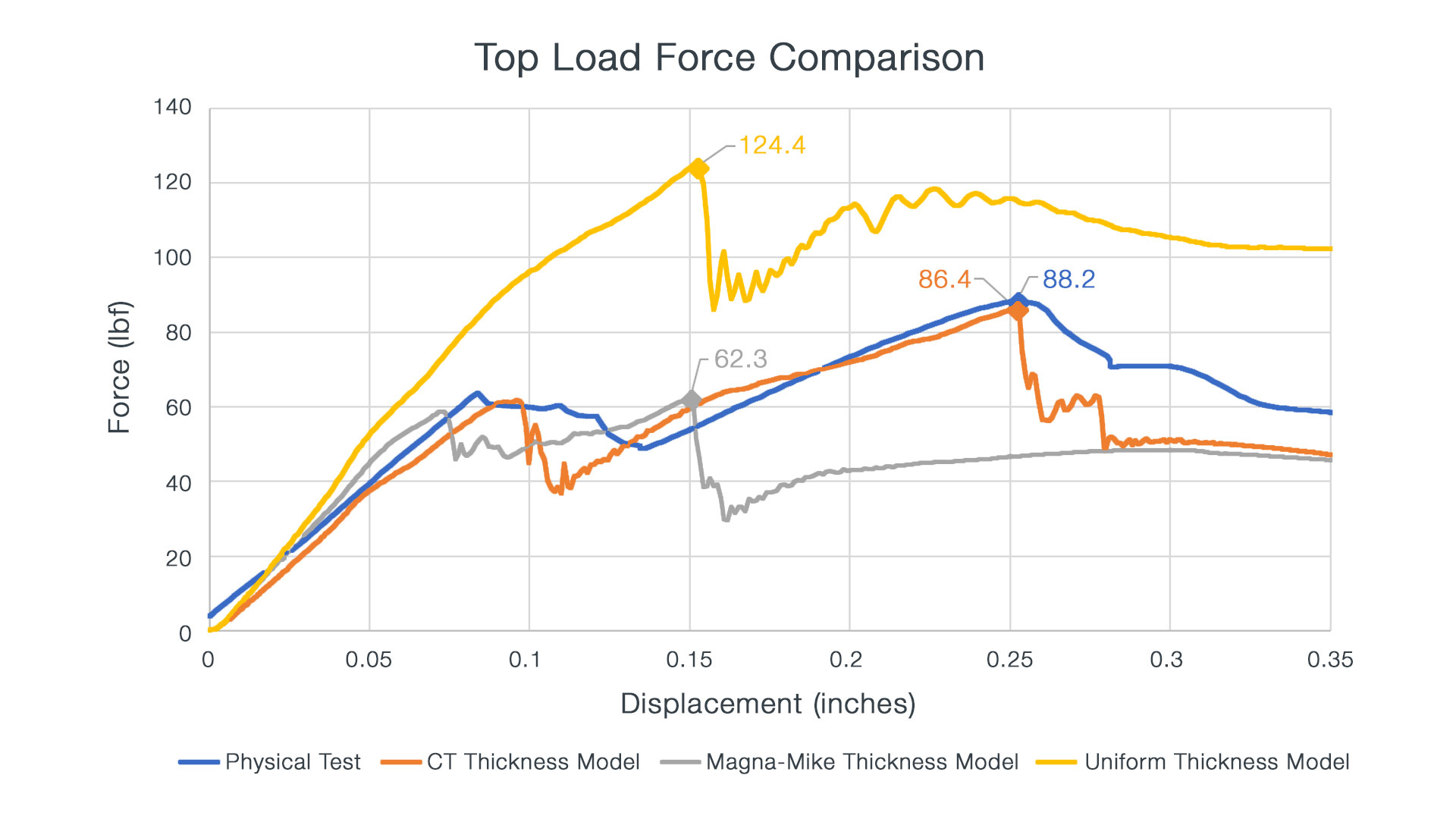
The video below compares the bottle buckling behavior between the physical test specimen and the three bottle wall thickness modeling approaches. The high correlation between the 3D CT scan thickness model and test specimen buckling modes, and extreme deviation of the other two modeling methods, demonstrates the benefits of simulation validation processes.
Simulation Validation: Water Container Drop Test
In this example of simulation validation, high speed video of extrusion blow molded HDPE container drop tests were captured and used to validate Drop Test Simulation models. The simulations duplicated several container design specifications including: drop, top load, pressure, and shipping. Validated models were leveraged to optimize bottle weight, wall thickness, and material selection.
Kinetic Vision's high speed video capabilities include 16 mm, 22 mm and 35 mm lenses and capture rates up to 24,000 frames per second. Video is captured directly to a personal or laptop computer for in-field frame-by-frame evaluation and editing.
Simulation validation creates the ground truth to enable modeling and simulation to accurately drive product development. In addition, it also encourages bidirectional feedback between M&S staff and test technicians, leveraging the knowledge gained by both. The result: a better understanding of your product or system performance, both physically and analytically. Learn more about Finite Element Modeling and FEA Material Properties, and more about simulation validation at Wikipedia.