Innovate faster with a digital-first approach
Published Monday September 23, 2024Kinetic Vision is proud to have contributed to the September issue of the Journal of Blow Molding. Our article, starting on page 6, explores key innovations in blow molding and how a digital-first approach is transforming the industry. The need for innovation is growing, especially in creating sustainable and cost-effective packaging solutions. We are leading this transformation by accelerating product development through simplifying design, prototyping, and validation. By combining immersive design, predictive simulation, and rapid functional prototyping, companies can bring products to market faster, use materials more efficiently, and ensure top performance—all while boosting sustainability.
Immersive design
Immersive design has transformed industrial design by combining traditional knowledge with modern trends. In the past, packaging concepts were created through time-consuming hand-drawn sketches. The shift to 3D computer-aided design (CAD) made this process faster, moving from pencil and paper to digital tools. Immersive design has taken this further. With VR headsets, designers can now interact with their creations in 3D. This allows them to explore form and function in a more dynamic and life-sized environment. It speeds up the ideation process, helping designers move beyond static sketches to experience something close to the final product. In the past, creating physical models took a lot of time. Now, modern 3D printing technology allows the rapid creation of realistic prototypes. Innovations like those from Stratasys enable the production of multi-colored, transparent models within days. This significantly reduces the time and effort needed to go from concept to prototype.
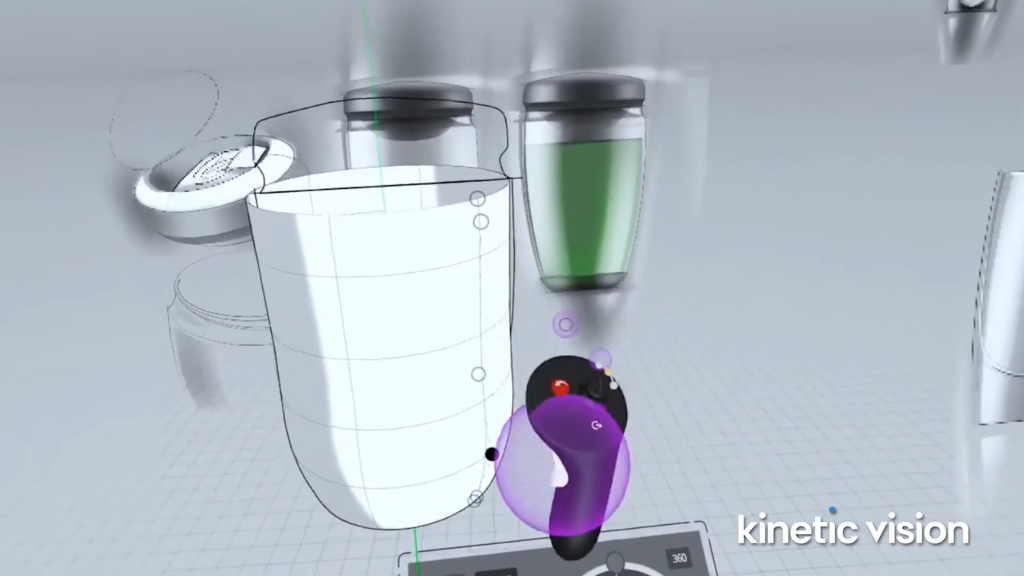
Predictive simulation
Predictive simulation is vital for validating new product designs, ensuring they meet manufacturing and consumer requirements while minimizing risks. Unlike traditional physical testing, which can delay product launches, virtual simulations enable rapid evaluation of design performance under various conditions. For blow-molded beverage packaging, simulations help identify potential issues in production and filling processes, avoiding costly disruptions. Advanced simulations, including real-time bottle conveying and lightweighting analysis, allow for quick adjustments to optimize design and reduce material use, ultimately saving time and costs. Kinetic Vision’s expertise in predictive simulation ensures accurate, efficient product development, achieving up to 30% material savings and enhancing both profitability and sustainability.
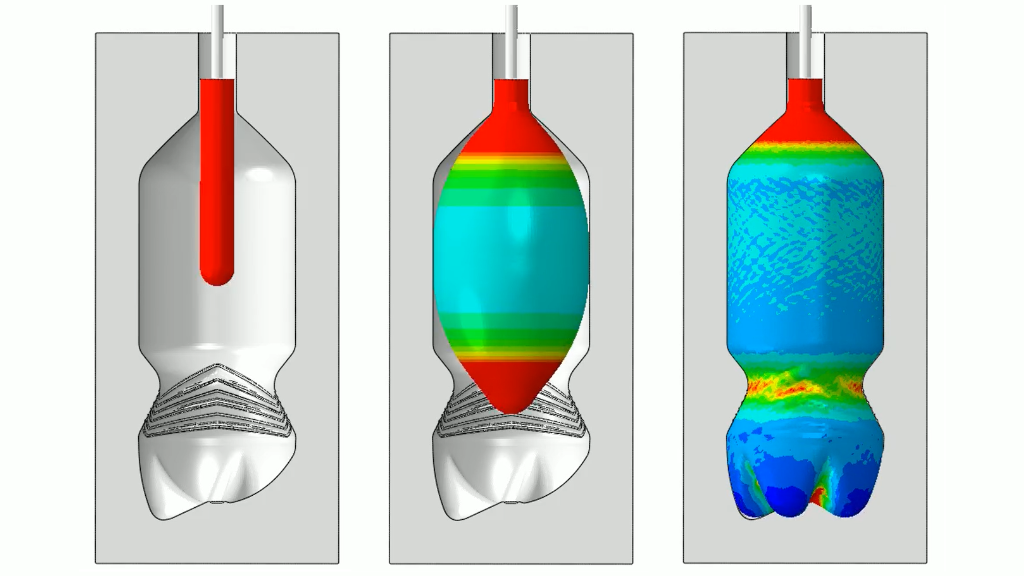
Rapid functional prototypes
Rapid functional prototypes have dramatically accelerated product development in the beverage industry. Traditionally, creating blow-molded bottles using injection stretch blow molding (ISBM) required several weeks or months to develop metallic molds and produce prototypes. However, recent advancements have transformed this process. By utilizing 3D-printed molds with metal casings, a leading food and beverage company can now produce blow-molded prototypes in just a few days. This shift from legacy methods has reduced development timelines by 30-50%, turning what once took months into a matter of days. With overnight multicolor 3D printing and simulation-driven design optimization, companies can move from initial sketches to functional prototypes in under a week. This rapid innovation not only speeds up the creation of engaging and sustainable packaging but also contributes to significant reductions in plastic waste. Optimized beverage packaging potentially could eliminate the equivalent of hundreds of billions of bottles from landfills annually.
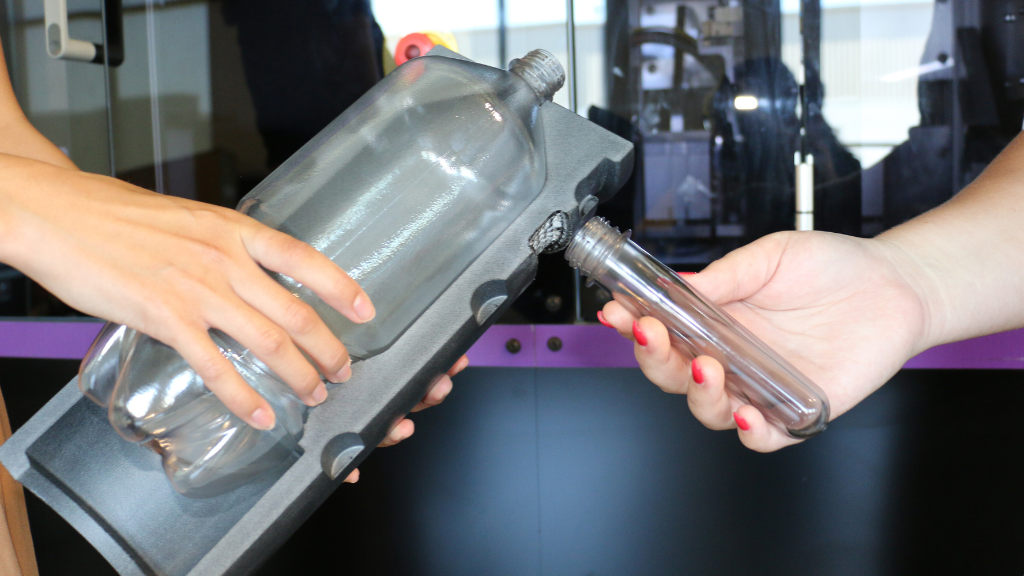